SWRO Membranes Go Vertical in Israel
After passing its performance testing, Israel's new Sorek large-scale desalination plant is now operational. For the first time globally, the plant features 16" SWRO membranes in a vertical arrangement. The article looks at claims that "going vertical" can reduce a plant footprint and CAPEX costs.
Back in 2000 when the Israeli governmental agency Water Desalination Administration (WDA) launched the Desalination plan, it would have been hard predict that 13 years later it would have paved the way for a revolution in membrane desalination.
Since that report, Israel's desalination landscape has changed dramatically. In 2005 the Ashkelon 330,000 m3/day reverse osmosis (RO) plant was commissioned, later being expanded by 20% to 392,000 m3/day.
Four years later in 2009 and the Hadera 465,000 m3/day RO plant was commissioned, delivering what was considered at the time to be one of the lowest prices of potable water.
While Ashkelon and Hadera could be considered large scale projects, especially for membrane SWRO, the biggest was yet to come.
Raising the bar in Sorek
Four years later in October 2013 the Israeli company IDE Technologies opened the doors to its Sorek plant for testing, claiming it is the "world's largest and most advanced SWRO (seawater reverse osmosis) desalination plant". The facility has the capacity to produce 624,000 m3/day (150 million m3/year) of potable water and is located 15 km south of major city, Tel Aviv. At the end of November, Sorek had passed its final performance testing and was already producing full capacity.
The 25-year BOT (Build-Operate-Transfer) contract for the project was awarded to the Sorek Desalination Company (SDL). This is a single purpose entity set up for this project, led by IDE Technologies with a 51% share and Hutchison Water International Holdings with the remaining 49%.
The basic concept for the construction of the 150 million m3/year plant is to have two 75 million m3/year plants able to operate separately from and independently of one another.
Most large scale RO systems comprise horizontal arrays of multi element vessels with six, seven or even eight elements of 8" diameter mounted in a series. The system proposed for Sorek uses 16" BEL elements in a series, but rather than the conventional horizontal arrangement, these are mounted vertically.
The thought behind this is that usually the rack support requirements to house much heavier 16" elements are considerate, given the additional weight.
By instead installing them upright, fewer frameworks are needed to support the vessels, as well as pipes and fittings. Construction and installation of the membrane elements changes as well with the loading of the elements done automatically.
Cleaning up
Patenting this vertical arrangement, IDE says this could pave the way for future SWRO plants. They claim it means lower investment costs "due to decreased construction area and piping headers", higher plant efficiency and a reduced footprint (50% compared to traditional RO).
The Israeli firm believes that switching the arrangement from horizontal to vertical will also have its benefits for membrane cleaning.
Dr Boris Liberman, chief technology officer of membrane technology at IDE tells WWi magazine: "Up till now, RO horizontal 8" membrane cleaning was done with detergent producing foam. This required washing the foam off the membranes and consumed more time and maintenance. The challenge became even bigger for horizontal 16" membranes. Once IDE came up with the patent of 16" membranes in a vertical array, this challenge (washing off the foam) was resolved, increasing availability, while saving time and costs."
Speaking to WWi magazine, Dr Graeme Pearce, principal at Membrane Consultancy Associates, says that with this arrangement "there is then a much greater burden on the elements and vessels themselves, and significant strength is required in the element core tube to ensure that the element can support its own weight as it is loaded into the vessel".
He says: "The core tube of a 16" element therefore has a much greater load bearing duty than an 8" element and the first generation of these elements have used GRP rather than plastics such as PVC or ABS. Cost is therefore transferred from the system builder to the element maker."
"Beefed Up Element"
Responding to the question of whether a "greater burden" on the vessels could lead to a decreased life expectancy, Pearce adds: "It is possible that if stresses were too much you might get an early catastrophic failure, but as I understand, the element makers for the first project are going for a much beefed up element.
"This adds quite a bit of cost to the element and they may be looking to reduce this cost add on in future generation of 16" membranes."
He goes onto say: "You might expect 16" elements to be quite a bit cheaper than 8" due to the economy of scale, but I think the cost add on of the higher strength core tube takes up quite a bit of the saving.
"However, the system cost saving is determined just as much by savings in vessels and pipework as savings in elements, so a 16" system whether horizontal or vertical would have a decent cost saving over an 8."
Leon Awerbuch, president and CTO of Leading Edge Technologies and director at the International Desalination Association (IDA) remains optimistic about the vertical set up.
"If after time, information about the practical aspects of this approach can be verified, I think we could expect to see it in use in other plants," he says. "I would expect to see it used only in large plants and only if practical experience proves that handing of the elements is not an issue. Otherwise, this looks like a great idea."
Awerbuch says that by opting for 16" membranes, they have more "membrane area" and, as a result, produce 4.3 times more desalinated water than an 8" element.
He adds: "This approach allows a significant reduction in plant footprint, shorter and smaller diameter HP pipes and an improved membrane loading method. In addition, due to the larger volumes of feed water, this design reduces membrane fouling and polarization."
IP Protection and Price
Making claims about footprint and CAPEX savings, Sorek's vertical membranes will surely attract the eyes and the ears of the global desalination community.
This raises the question of what's stopping other desalination suppliers/plant operators copying this set up? In short, IDE has it heavily patented and protected.
Are they expecting companies to find a way around the patent?
"We believe not," says Liberman. "IDE's patent is not only about the vertical positioning, but rather around the technical features that enable operation in a vertical array."
The technology is patented with several applications pending in major markets such as the US, Australia, China and Europe but not in MENA (except for Israel itself).
Awerbuch adds: "It's not that easy to bypass the patented technology elsewhere – knowing about the technology doesn't necessarily translate into the ability to make it patentable."
It's important to note that, like with its installations at Ashkelon and Hadera, IDE has installed features such as dual media gravity filters, and a pressure centre concept for high pressure pumps and energy recovery devices, in addition to a membrane-based boron removal arrangement. This will achieve a maximum boron limit of 0.3 mg/L.
In terms of the cost of water produced in Sorek, its currently $0.68/m3 compared to a bid price of $0.58/m3. This compares to $0.89/m3 (bid price $0.57/m3) for Hadera and $0.95/m3 (bid price $0.52/m3) for Ashkelon.
Israel has the goal to produce 650 million m3/year of desalinated water by 2020. With the country possessing only 265 cubic metres per year of freshwater available per person, this is well below the U.N. definition of water poverty (below 1000 cubic metres per person). As a result, desalination will continue to be the major part of the country's water supply.
If successful, and the number of large scale SWRO plants keeps increasing globally, then it might not just be Israel where vertical membranes are being proven.
Tom Freyberg is chief editor of WWI magazine, for more information email: [email protected]
FAST FACTSCAPACITY: 624,000 m3/day If after time information about the practical aspects of this approach can be verified, i think we could expect to see it [vertical Ro modules] used in other plants |
About the Author
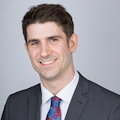
Tom Freyberg
Tom Freyberg is an experienced environmental journalist, having worked across a variety of business-to-business titles. Since joining Pennwell in 2010, he has been influential in developing international partnerships for the water brand and has overseen digital developments, including 360 degree video case studies. He has interviewed high level figures, including NYSE CEO’s and Environmental Ministers. A known figure in the global water industry, Tom has chaired and spoken at conferences around the world, from Helsinki, to London and Singapore. An English graduate from Exeter University, Tom completed his PMA journalism training in London.