Rinse and repeat: How flow reversal greatly extends the life and performance of reverse osmosis treatment plants
Now that the U.S. EPA has issued official Maximum Contaminant Levels (MCLs) for PFAS in drinking water, all eyes are on mitigation technologies as municipal water treatment systems seek effective solutions. While reverse osmosis (RO) is considered a best available technology for PFAS removal due to its ability to trap both short- and long-chain PFAS, its appeal has been limited by a typical recovery rate of about 75%. Facilities that attempt to increase recovery rates with conventional RO will experience numerous operational issues, such as increased energy cost and mineral scaling, which leads to more frequent membrane cleaning and a shorter membrane life span. Expensive, anti-scalant chemicals are therefore required to inhibit and moderate the effects of membrane scaling and fouling.
Reversing the flow is a game changer
ROTEC’s proprietary Flow Reversal Reverse Osmosis (FR-RO) technology enables a high recovery rate (90 to 95%) without increasing membrane cleaning, membrane replacement or chemical applications. This patented technique decreases the amount of feed water that requires pumping and significantly diminishes the volume of contaminated wastewater, reducing energy, maintenance and disposal costs and increasing sustainability.
FR-RO technology employs two techniques to reverse osmosis: flow reversal and block rotation.
Flow reversal is the periodic reversing of the flow direction of the treatment stream, which prevents scales from forming on membranes. It allows an increase in product water capacity relative to the amount of feed water, typically achieving 90 to 95% recovery without an increase in energy demand.
By periodically switching the flow direction, scale does not have time to form on membrane surfaces before being swept away by under-saturated feed solution conditions. The frequency of switching is dictated by the time it takes for a supersaturated solution in the concentrate to grow a population of scale particles that can allow continued scale growth. By using the under-saturated feed to resolubilize the nascent scale particles in the concentrate before they exceed a critical size, extensive precipitation is prevented. This approach enables much higher RO recovery rates than can be achieved with anti-scalants alone.
In a conventional single pressure vessel using RO membranes, the feed becomes more concentrated as treated water exits the membrane. As the recovery gets higher, scale will begin to form on the surface of the membrane. With traditional RO this would require the system to be shut down for cleaning. In a flow reversal system, before the scale gets firmly established on the membrane surface, the direction of flow is reversed, thus cleaning the membrane of any scale that started to form.
The other chief component of FR-RO is block rotation, which inhibits scaling by staging the membranes into a series of blocks that cycle through a rotation where each block takes a turn as the last stage of the system. Much like rotating the tires on a car, this technique moves the membranes out of the worst position before scaling can take hold. When the last stage block switches back to the first stage, the flow is reversed and undersaturated feed water dissolves any scale particles before they can proliferate.
The economic benefits of flow reversal
Flow reversal reverse osmosis offers several benefits to water treatment facilities. First, it allows for greater recovery rates, typically around 95%. However, in installations with a higher quality of influent water, the recovery rate can be as high as 98%, making RO an attractive solution for public water systems. This also represents a 50 to 80% reduction in concentrate volume and a major improvement in wastewater management.
It also reduces and/or eliminates the costs associated with scaling, such as membrane cleaning, chemical purchasing, storing and handling, premature membrane replacement and associated personnel time. And it minimizes the risk of unscheduled cleaning and unexpected downtime, with all the related adverse impacts and expenses of those events.
For plants already using RO, an FR-RO system operates like a conventional RO and can easily be added as a retrofit with complete fallback. If, for whatever reason, the plant wants to revert to a conventionally operating RO system, operators can simply refrain from stroking the valves. And with no requirements for special operator training, proprietary hardware or specific membranes, introducing a new system or upgrading an existing system from any manufacturer to flow reversal has a low barrier to entry.
How flow reversal reduces long-term RO costs for PFAS mitigation
Because of the traditional low recovery rates, RO has not been an attractive solution for water treatment plants, for which a 25% hit on treated water output is unacceptable. Flow reversal changes all that, by frequently reducing loss to as lttle as 5% while also offering better PFAS mitigation and low long-term costs when compared to granular activated carbon (GAC) and ion exchange (IX). As compared to both GAC and IX, FR-RO offers an improved ability to capture both short- and long-chain PFAS, resulting in drinking water that is safer for human consumption.
Compared with GAC, FR-RO has lower operating costs because GAC requires more frequent media changeouts as well as higher disposal costs of spent media. With flow reversal, membranes last much longer, and the waste stream is a small volume of PFAS-concentrated liquid, which can be treated with a small amount of GAC (a tenth of what a plant would use in water treatment) before its return to the environment. Compared to IX, FR-RO treats a wider range of contaminants and has lower operating costs due to savings on media. Drinking water plants looking at a 20-year equipment life cycle can reap economic benefits by choosing a flow reversal RO system.
FR-RO future proofs a drinking water facility's containment strategy
As history continues to teach us, PFAS will not be the last emerging drinking water contaminant of concern, with the recent MCL announced by the California State Water Control Board for hexavalent chromium as a prime example.
A major benefit of RO is that its membranes can remove much smaller particles than other technologies. Water treatment plants can reduce their risk of future exposure to new contaminants by investing in reverse osmosis, and with flow reversal technology, they can count on an RO system that will sacrifice less water to waste and enjoy extended membrane life with less maintenance.
Another aspect to consider with any PFAS mitigation technology is what happens to the PFAS that are removed, whether they are trapped in GAC media, IX media, or RO wastewater. For the time being, GAC and IX media must be sent off for incineration, and there is some evidence to suggest that incinerating media can result in transferring PFAS to the air as plume gas, where it can eventually find its way back into human bodies through water or air.
In fact, when considering thermal treatment technologies (incineration) for PFAS disposal, the Department of Defense recognizes “that these options have higher levels of uncertainties regarding their capacity to control the migration of PFAS into the environment.” Some plants landfill their spent media, where leachate is known to return contaminated water back into the watershed.
While FR-RO does not completely solve the problem of PFAS-contaminated waste, it does condense it into such a small volume of liquid waste that a water treatment plant can treat its contaminated wastewater using just 1/10th of the amount of GAC it would typically use for water treatment. By using FR-RO to treat the water and GAC to treat the resulting wastewater, a plant can achieve a sustainable and future-ready operation.
Consider also promising new PFAS treatment innovations such as foam fractionation, which condenses the PFAS waste volume even more. The industry can further reduce the cost of PFAS treatment, destruction and disposal through exploration of these novel technologies and solutions.
Two birds, one stone
Water contamination is not the only major challenge facing water treatment. Another is the increasing uncertainty of water availability in many parts around the world as climate change causes droughts, floods and other threats to water quality and security.
RO has brought desalination to the mainstream, especially in coastal areas most vulnerable to rising sea levels and extreme weather events. It has provided a lifeline for communities that would otherwise have to abandon their homeland because of water insecurity. Where source water is heavily loaded with salts, organics and/or toxins, RO is often the only option, and with the addition of flow reversal, communities can spend less on energy, chemicals and media.
Case study: santa monica uses FR-RO to become water self-sufficient
As part of its journey to become water self-sufficient by 2023, the coastal city of Santa Monica, California, upgraded its Arcadia Water Treatment Plant with a $200 million investment. Part of its vision was to increase supply from this plant from 50% of the city’s water supply to 60 to 65%, by increasing the desalination plant’s recovery rate to 90%.
Engineering consultant Brown & Caldwell chose ROTEC’S flow reversal technology as the most suitable for this flagship project and collaborated with Walsh Construction to deliver the plant’s retrofit design and execution in a progressive design-build approach.
After a successful pilot in 2021, Arcadia moved to the next phase of retrofitting the entire brackish water RO plant with this technology. To enable the plant to continue producing drinking water during construction, the plan called for incrementally retrofitting each of the facility’s four RO trains, which together treat almost 11 million gallons per day (MGD).
Following the retrofit, the facility recovery rate increased from 82% to more than 90% with stable performance, greatly reducing the amount of water that goes to waste. For every 10 gallons of groundwater treated, 9 gallons of drinking water are produced, a significant improvement over the 8 gallons produced by the previous system. This is critical because groundwater is a limited resource, and any waste of that valuable water makes self-sufficiency more challenging.
Thanks to flow reversal technology, the Arcadia Water Treatment Plant allows higher generation of clean water, utilizing less raw water and dramatically reducing brine volumes. Flow reversal also minimizes operating expenses, chemical use and clean-in-place (CIP) events, leading to a more sustainable, affordable and eco-friendly water treatment approach.
Case study: FR-RO delivers water autonomy and security for the Daru people in Papua New Guinea
With about 20,000 residents, the island of Daru in Papua New Guinea previously imported its water from a diesel-powered pumping station located on the mainland. This was an expensive source and supply was unreliable, often leaving the island stranded with no available potable water for months at a time.
Lacking water independence and facing potential fuel shortages and other logistic challenges, the island needed a solution to provide a reliable clean water supply for its communities and agricultural development.
The PNG Sustainable Development Program and Innovative Agro Industry, an affiliate of the international development company LR Group partnered with ROTEC to deliver a water project that combines green energy and clean water supply to Daru.
The plant treats borehole brackish water of such low quality and high salinity that it does not meet World Health Organization regulations but was ultimately no match for the FR-RO process. By using this technology, the Daru project delivers water recovery rates of 80 to 90% while using near-zero chemicals in the process, all while maintaining high performance and minimizing impact on the marine environment.
The 507,210-gallons-per-day turnkey water treatment plant was commissioned in a record two months, despite facing challenging logistics, including delivering materials and equipment to a remote island. It provides Daru’s inhabitants with more than 0.5 MGD of high-quality drinking water per day.
By linking to a neighboring solar array and utilizing FR-RO technology, the plant eliminates high diesel fuel costs and reduces the carbon footprint associated with water production. Thus, Daru is a project that demonstrates the power of green desalination.
About the Author
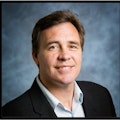
Bruce J Alderman
Bruce J Alderman is a passionate, process-driven leader with a proven record of bringing new products to new markets. He built and led a team of sales, process and product specialists that brought a disruptive water product to global industrial and municipal markets. In 6 years, Alderman sold more than 200 systems to more than 50 companies and successfully penetrated the municipal market with 16 MGD system scale. Alderman led the process to complete the sale of Desalitech to DuPont in Janurary 202o in a competitive bidding process and the followinf integration into DuPont. He is currently the CEO of ROTEC USA.