Optimizing Pumping Systems in Drinking Water Distribution
Water is vital for our daily lives – for drinking, washing, generating energy, and growing the food we eat. The need to improve water management and resilience is obvious. It is estimated that the United Kingdom will need an extra 4 billion liters of water daily by 2050 to ensure that the water network is resilient. Careful management of the drinking water network is vital to efficiently deliver water to consumers. There are crucial components of a drinking water distribution system, and certain factors, such as varying demand, available water supply, environmental sustainability, financial implications and the possibility of energy cost reductions must be given careful consideration. There are also opportunities for improving pumping system performance to prevent water leaks and reduce utility operating costs.
Crucial Components
There are five main components of a drinking water pumping distribution system: hydraulic pumps, motors, piping, valves and end-use equipment. Pumps are available in a wide range of types, sizes and materials and classified according to two main categories: positive displacement pumps or centrifugal pumps. The latter offers benefits such as lower cost, simplicity of use, safety, lower maintenance, fewer parts and a longer operating life. Most pumps are driven by electric motors for municipal applications. In special cases, pumps may be driven by diesel engines to allow them to operate during a power outage.
Piping, used to carry water to the point of use, is an important consideration of a drinking water pumping distribution system. Friction loss (where water flowing in a pipe loses head, pressure, or energy as a result of friction) is one area that can cause issues. Factors which can affect friction loss include pipe diameter, pipe material roughness, pipe length, flow rate and water viscosity. For instance, bigger pipes are more difficult to route but present less flow resistance compared to smaller pipes which are much more flexible to route but may present higher resistance and friction.
Another important component of a pumping system are valves. Valves are used to regulate flow (e.g. throttle or bypass), to isolate equipment or to allow water to move in only one direction (check). When selecting an appropriate valve for a specific project it is important to think about the frequency with which the valve will be activated (closed/open), in addition to the reliability of the technology, leakage tendency, ease of maintenance and cost. Final considerations should also be given to end-use equipment such as taps, tanks, etc.
Improving Pumping System Performance
There are three areas which offer an opportunity to improve the system performance. The initial design phase is very important, including the selection of the pump itself. Next, it is essential to consider any improvement needs during operation, and finally, there are opportunities for improvements when system requirements change.
Correct sizing of pumps is vital to avoid problems and inefficient operation. Good selection practices include determining the working conditions, estimating possible future demands, determining the technical and economical fit of the solution, and looking ahead to any system or remote monitoring requirements. In many cases pumps are sized according to the pressure and flow requirements of the network with respect to time of day and time of year. If heavy variations occur, designers generally size with worst-case scenarios. Crucially, the assessment of the system requirements must be done with the utmost care and diligence. Consideration should also be given between a single pump vs. a booster set. Instead of one large pump, a booster set employs smaller pumps which save energy during low demand periods. It is possible to adapt the performance according to system demand.
There are potential savings that can be achieved from efficient pumping systems. System optimization is a crucial factor, for instance ensuring that everything is sized correctly, valves are in good working order, and ensuring everything is designed efficiently with minimum friction loses. Systems with high annual operating hours bear high operating and maintenance costs. Up to 40 percent of the potential savings in a pumping system could be reached through higher efficiency equipment and the use of a variable frequency drive (VFD). Speed reduction provides significant energy savings at partial load. Variable frequency drives offer a reduction of the energy cost between 55 and 75 percent, and a reduction of the maintenance cost between 20 and 35 percent. The aim is to operate the pump in the range of the best efficiency at variable speed operation.
Avoid Leakage and Optimize the Pumping System
Water leaks and structural weaknesses in pipes are a sign that a drinking water network could soon fail. Leaks reduce the reliability of the water supply network and if undetected, such leaks may contribute to future pipe failures. Another important point is that such leakages trigger an important loss of resources, both in terms of water and energy.
As previously mentioned, pump oversizing can contribute to leaks. Pump oversizing often occurs due to the need to withstand peak loads, but it results in higher energy bills, higher operating costs, higher wear on all the components of the system, higher maintenance costs, less system reliability and lower efficient operation. A non-adequate selection added with other installation and design defects may cause leakage at mechanical joints of the pipes and pumping system, due to inadequate support, vibrations and valve problems. In addition, a well-controlled operation of the pump with intelligent VFD reduces the water pressure when water demand is lower and prevents hydraulic stressing on the aging piping infrastructure. For example, simple soft start of the pumps eliminates hydraulic hammering in the pipe, which are causes to dislocation of the joints and weakening of the wall material. Improving piping configuration can help tremendously. One best practice would be to determine proper size, minimize pressure drop, select low-loss components, keep the pipes as linear as possible and put valves and equipment in line with the pipe run.
Additional pumping system issues include inefficient system operation, excessive maintenance requirements, erosion of components, and cavitation. Signs of an oversized system include excessive flow noise, heavily throttled flow control valves, heavy use of bypass lines, frequent replacement of bearings and seals and intermittent pump operation. Remedies include VFDs, smaller impeller or impeller trimming or smaller pumps.
A Final Thought
By working together, it is possible to solve the toughest water challenges, energy consumption demands, quality monitoring needs, productivity, operational challenges and safety issues. Solutions must be energy efficient, reliable and compliant with the applicable regulations, standards and codes. WW
About the Author: Paul Winnett is general manager for building services and industry for Xylem Water Solutions. Having worked in the Building Services and Industrial business at Xylem for over 30 years, Winnett brings a wealth of experience and knowledge in the customization of solutions for applications and designs to be on the latest trends in these markets. He has built up a strong background in best practices regarding large scale building and industrial projects, and has also sat on various British Standards committees to help initiate some of these best practices into today’s standards.
About the Author
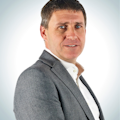
Paul Winnett
Paul Winnett is general manager for building services and industry for Xylem Water Solutions. Having worked in the Building Services and Industrial business at Xylem for over 30 years, Winnett brings a wealth of experience and knowledge in the customization of solutions for applications and designs to be on the latest trends in the Building Services and Industrial markets. Having worked on a number of large scale Building & Industrial projects, he has built up a strong background in best practices and has also sat on various British Standards committees to help initiate some of these best practices into today’s standards.