Located in Southwest Ohio, Greater Cincinnati Water Works (GCWW) supplies more than 43 billion gallons of water a year, utilizing a surface water plant equipped with eight raw water pumps capable of producing 240 million gallons per day, a ground water plant utilizing 13 wells capable of producing 40 million gallons per day, and 94 finished water pumps supplying water to 1.1 million customers.
The western service area of the system is partially supplied by the Western Hills Pump Station (WHPS), which is a major booster pump station within the GCWW system. The current pump station was completed in 1937 as a replacement for a smaller pre-existing station, and to meet the increasing demand of the area. The original pump station was built in 1907, but by 1930 was operating at max capacity and a larger station was required. Years of debate and analysis were taken to determine if the new station should be steam operated or electrified, as all of GCWW’s pumps were steam driven at that point. Ultimately the utility settled on electrification of the station.
Detail was not limited to just the exterior of the building. Ivory terracotta tile covers the walls, which are topped with ornate plaster inlays and chrome trim. Spread across the pump floor are five, two stage De Laval Double Suction pumps with a combined capacity of 40 MGD. Each pump is trimmed with polished brass accessories to match the design of the building. Massive windows allow natural light to enter and reflect off nearly every surface.
Working routinely in a building of this caliber led GCWW Machine Shop to turn a recent pump rebuild into much more. Pump Unit 4 is a two stage De Laval pump that has been in front line service since November 17, 1937. Low efficiency, reduced reliability, and predictive maintenance assessments led to discussions and planning for the future of this pump unit. Total replacement was considered, but high replacement costs and extensive piping reconfiguration would be required. Budgetary estimates for a replacement two stage pump were in excess of $1 million. This quickly led staff to explore the total refurbishment of the pump unit.
Refurbishing a pump of this age would lead to many challenges, such as obsolete pump components, coordination with machining vendors, and a limited window of time to return the unit to service. GCWW determined that to minimize these issues and create the highest quality work product the refurbishment would be completed in-house.
Despite the availability of skilled trades people diminishing every year, GCWW has continued a long-standing tradition of staffing a machine shop with manual machines and in recent years added CNC machinery. Having the capabilities to produce parts in-house greatly reduces dependency on vendors and allows for more rapid turnaround times. In addition to the machine shop, the GCWW maintenance section also includes a weld shop, carpentry shop, facilities maintenance group, and paint shop; all of which were able to contribute to the overhaul.
From the beginning of the refurbishment, maintenance staff took the opportunity to not only pay tribute to the craftsmen who constructed the building and maintained its mechanical assets for over 80 years, but to showcase the talents of the highly skilled trades people that GCWW employs.
WHPS was staffed 24 hours a day until the mid-‘90s when more modern automated controls were installed. While staffed, one of the weekly tasks included hand polishing the bright work on each pump. As on-site staff decreased, this practice was abandoned. Much of the elegance and appeal of this equipment was the high level of detail originally applied to each pump. Staff were able to restore the original bright work and original pressure gauges were disassembled, hand polished, and returned to operational condition. Over 100 individual fittings, lines, and accessories were cleaned, inspected, and hand polished. Once brightwork polishing was complete, a clear coat was applied to each to maintain the shine for years to come.
The overhaul of Pump 4 provided an opportunity for GCWW staff to keep an aging asset in service well beyond its expected lifespan, as well as provide a team building experience that was greater than a pump overhaul would typically provide. Every group that worked on the pump overhaul was able to showcase their abilities and share in the experience of refreshing a historic piece of equipment that will continue to serve GCWW’s customers for decades into the future. WW
About the Authors: Justin Barkey is a plant maintenance supervisor at Greater Cincinnati Water Works in Southwest Ohio with over 20 years of mechanical maintenance experience. He manages pump station maintenance, capital valve replacement, and the utility’s pressure regulator program.
Greg Roa, P.E., is a Supervising Engineer with the Greater Cincinnati Water Works with over 22 years of experience in utilities industries. He manages mechanical and facilities maintenance as well as capital projects for the utility’s supply division.
About the Author

Justin Barkey
Justin Barkey is a Plant Maintenance Supervisor at Greater Cincinnati Water Works in Southwest Ohio with over 20 years of mechanical maintenance experience. He manages pump station maintenance, capital valve replacement, and the utilities pressure regulator program.
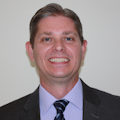
Greg Roa
Greg Roa, P.E., Fe is a Supervising Engineer with the Greater Cincinnati Water Works with over 22 years of experience in utilities industries. He manages Mechanical and Facilities maintenance as well as capital projects for the utilities’ supply division.