Addressing the Challenge of Zoogleal Film Buildup
Located in southeast New Mexico, close to the Texas border, the City of Hobbs’ wastewater reclamation facility provides uninterrupted wastewater treatment for the community, including liquid wastes transported to the facility. It serves over 43,000 people and is currently receiving and reclaiming about 3.2 million gallons of wastewater a day.
The Hobbs Wastewater Reclamation Facility (WWRF) has been twice awarded the Max Summerlot Award, the State of New Mexico’s highest and most respected industry award, presented annually to the New Mexico water or wastewater facility that demonstrates the highest level of professionalism and excellence in its operation, maintenance, management, and safety.
The plant processes approximately 95 percent residential wastewater, with the remaining 5 percent composed of light industrial wastewater. After treatment, 70 percent of the effluent is used by local farmers for irrigation and the remaining 30 percent is used by the city for irrigation of local public parks and sports facilities.
Potable water for the city is drawn from the Ogallala Aquifer before being treated and used by the residents and light industry. Given the arid climate, Hobbs has low measurable rainfall, so the reuse of all wastewater is critical for sustainable irrigation by the city and local farmers.
Process Overview
The plant is classified as an activated sludge, biological nutrient removal (BNR) facility employing the Modified Ludzack-Ettinger (MLE) activated sludge process, with nitrate removal in three parallel trains. In each train, after initial grit screening, the effluent goes through an anoxic zone, comprised of four basins, where nitrates are removed through bacteria in a low oxygen-starved environment, utilizing molecular oxygen from the nitrate molecule and releasing harmless nitrogen that bubbles to the surface.
In this process, optimal performance is achieved by keeping dissolved oxygen levels at the 0.1 to 0.3 mg/L level. Bacteria are constantly introduced through activated sludge and mixed liquor suspended solids returns from the end of the process.
The next part of the process involves the effluent from the anoxic zone flowing into the first of three aeration basins located in a series, where bacteria is used to break down and consume organic matter that forms clumps of suspended solids. The biological oxygen demand (BOD) of this process is key and oxygen is pumped into these aeration basins continuously from large blowers located in a building next to the aeration basins.
In each basin, the dissolved oxygen levels are maintained at a fixed level to optimize the breakdown of the organics in the wastewater. Basin 1 maintains a 3 percent dissolved oxygen level, Basin 2 maintains 2 percent, and Basin 3 maintains less than 1 percent. This process has many benefits, including the significant reduction in effluent odors, which together make the facility’s location near a residential area a non-issue.
Final Treatment, Solid Waste Removal, and Water Reuse
Once the wastewater has passed through these aeration basins, it is sent to three final clarifiers, where the suspended solids settle to the bottom.
This return activated sludge (RAS) is returned to the front of the anoxic basins where it mixes with internal recycle sludge and incoming wastewater. The clarified water leaves the clarifier, and gravity flows through UV channels and a mild chlorine treatment to a holding pond before being pumped to the farm, parks, and a cemetery for irrigation. The solids are removed, aerobically digested, dewatered and 100 percent is reused for soil amendment by the city, its residents, and farmers.
Reliable Dissolved Oxygen Measurement
Tight control of the dissolved oxygen (DO) levels is critical to the optimal performance of the plant. Accurate DO measurement in the aeration basins enable the multistage centrifugal blowers to be optimized to avoid wasting energy. This can save thousands of dollars per year in operating costs. More importantly, it also avoids over- or under-oxygenating the aeration basins that can significantly impact the bacteria’s effectiveness.
Too much or too little oxygen can reduce the bacteria’s ability to break down organic matter and nitrogen. Both conditions will negatively impact the operation of the wastewater facility. In extreme cases, over- or under-oxygenating can poison and kill the bacteria, leading to expensive and lengthy plant shutdowns as the whole MLE process has to be re-established, permit violations could be incurred, irrigation water has to be sourced elsewhere, and strong effluent odors become an issue in the surrounding residential area. Given that the rebuilding of the MLE process can take many weeks, this would be a major expense and environmental issue for the local community.
The Challenge of Zoogleal Film Build-Up
Zoogleal film is a natural occurrence in wastewater plants and consists of bacterial matter building up into a jelly-like mass or slime layer that coats plant equipment. It is especially a problem for DO sensors that are relied upon to measure the oxygen levels in the aeration basins and send that data back to the control room for plant operation and optimization.
Accurate control over oxygen levels in the basins is 100 percent reliant on accurate measurement by the DO sensors being used. If the measurements become unreliable, serious consequences can occur due to over or under oxygenating the basins — as described previously.
DO sensors are inserted into the nine aeration basins and measure oxygen levels 24/7. The City of Hobbs recently switched to optical sensors that utilize the dynamic luminescence quenching principle: a light-based measurement technique.
This technology is superior to electrochemical sensors, as they have no membrane or chemical components that wear out quickly and need constant re-calibration and maintenance. Over the years, the Hobbs WWRF used DO sensors from various suppliers and faced many challenges due to zoogleal film build-up.
Previously, treatment plant employees had to remove and clean its DO sensors every two days to avoid inaccurate readings. This process takes about 2 hours to clean all nine aeration basin DO probes; meaning that the facility was spending, on average, 20 hours per month or 240 hours per year cleaning DO sensors.
After installation of the ABB DO system, employees have their time back, only cleaning the probes once every 14 days. The plant is now saving 16 hours per month or 194 hours per year in labor costs that can be utilized elsewhere.
The ABB system at the plant is comprised of the Aztec ADS430 sensor and Aztec AWT440 multi-channel transmitter, and utilizes recent developments in optical measurement technology. The ADS430 optical DO sensor’s robust design means it not subject to problems that affect conventional membrane-based sensors, such as abrasion, fouling or poisoning.
The sensor is not affected by photobleaching or stray light and is also immune to the effects of sulfides, sulfates, hydrogen sulfide, carbon dioxide, ammonia, pH, chloride, and other interferences. This enables it to provide consistent, accurate readings over long periods of time without suffering from sensor drift. The ADS430 sensor is also constructed from inert, non-corrosive materials, making it suitable for use in high salinity environments.
Available in two and four channel versions, the Aztec AWT440 universal transmitter enabled the facility to connect four Aztec ADS430 DO sensors, enabling monitoring at multiple points without purchasing and installing separate transmitters. The facility’s previous supplier required one transmitter for each sensor, which increased purchase and installation costs, in addition to spare parts and maintenance.
This simplicity also extends to the sensor itself, which features a smart sensing cap with automatic setup. The SmartCap is capable of up to 24 months of continuous operation, greatly reducing the requirement for maintenance.
When cleaning is necessary after 14 days, probes can be cleaned and redeployed without calibration. To manage the zoogleal film in between cleanings, the sensor is kept accurate using ABB’s auto-cleaning system. This system periodically injects a high pressure burst of air across the sensor surface to remove the zoogleal film build-up. The ABB system uses small, packaged air compressors to achieve results that are controlled by the AWT440 multi-channel transmitter.
Overall, operators at the Hobbs WWTF are pleased with the ABB DO system. The community’s farmers, residents and city leadership team are happy, and the WWTF has more time to spend on managing other areas of the wastewater treatment process. WW
Published in WaterWorld magazine, January 2022.
About the Author
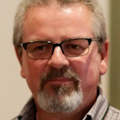
Peter Zacharias
Peter Zacharias is a senior utilities system specialist at the City of Hobbs, NM, Wastewater Reclamation Facility.