There's a new sheriff in town: LCRI takes over from LCRR as primary regulation for lead and copper pipes
To kick off a major reboot and fortification of the 1991 Lead and Copper Rule, the EPA’s Lead and Copper Rule Revisions (LCRR) was finalized in 2021 with the primary goal of requiring all public drinking water systems to create a Service Line Inventory (SLI) and to make that inventory publicly accessible by October 16, 2024. The SLI catalogs the material of every service line as non-lead, lead, galvanized requiring replacement (GRR) or unknown.
In addition, the LCRR required water systems to notify customers served by a lead, GRR or unknown service line by November 15, 2024, with annual notification thereafter, and in case of a systemwide lead Action Level Exceedance of 15 parts per billion (ppb), water providers must notify all of their customers within 24 hours.
This “stepping stone” regulation has prepared water systems for the final Lead and Copper Rule Improvements (LCRI), which arrived just before the LCRR compliance deadline last October. The LCRI takes additional steps to reduce lead exposure in drinking water by requiring water systems to remove lead-containing service line pipes in a 10-year timeframe.
The LCRI Has supplanted the LCRR
The LCRI essentially picks up where the LCRR left off and is now the primary regulation governing lead and copper levels in drinking water. Having focused on the LCRR for the last three years, water systems should be aware of the new requirements and deadlines of the LCRI. The provisions have several important impacts, with a compliance frontier that begins November 1, 2027.
Expanded and updated service line inventory — November 1, 2027
A new SLI submission, referred to as the “Baseline Inventory,” is due on November 1, 2027. This requirement pushes water systems to build on their initial service line inventory with the addition of connector materials (generally referred to as pigtails or goosenecks) to be categorized as lead, non-lead, unknown or no connector present. The connector material does not change the classification for the entire service line, although some states have different interpretations.
The EPA also wants water systems to continue eliminating “unknowns” from their inventories. Until otherwise classified, unknown service lines are treated as lead. This triggers a variety of disincentives in the LCRI including a greater public notification burden and forcing a more aggressive replacement rate for lead service lines (LSL) and GRRs.
A reduced lead action level from 15 ppb to 10 ppb — November 1, 2027
As in the LCRR, an Action Level Exceedance requires public notification within 24 hours, but at 10 ppb, the LCRI lead action level is much lower. A system wide action level exceedance also triggers a requirement to bolster corrosion control treatment and conduct public education.
Updated tap sampling protocol —November 1, 2027
Water systems with LSLs will be required to adjust their sampling protocol and sample for lead from both the first and fifth liter and use the higher value for compliance reporting purposes at LSL sites. This change has the potential to cause more systems to exceed the lead action level and be forced into additional requirements including corrosion control evaluations.
A list of all schools and childcare facilities the utility serves —November 1, 2027
Because of the greater risk of lead exposure to babies and children, the LCRI recognizes the heightened attention that schools and childcare providers should receive. The LCRI requires drinking water utilities to submit a list of every school and childcare facility they serve (and submit an updated list every five years) and send annual notification of the health risks of lead to every organization on the list. Water systems are also required to offer sampling, the details of which can be found here.
Validation of non-lead service lines — December 31, 2034
The EPA wants proof that non-lead service lines are truly non-lead and validation is required to be completed by December 31, 2034. Service lines that were installed after federal/state lead ban dates and lines that were previously visually confirmed as non-lead do not need to be reevaluated. A subset of the remaining lines classified as non-lead will be subject to confirmation via visual inspection.
Removal of all lead and GRR lines — December 31, 2037
Water systems that have LSL or GRRs will be required to replace those lines within 10 years - by the end of 2037. This aggressive replacement rate is another reason utilities should make a strong effort to properly classify their unknown service lines. In many cases those lines will be found to be non-lead, and it is much more expensive to replace a line than to determine what it is made of.
This list is not exhaustive but calls attention to the chief highlights. Complete details can be found on the EPA’s Lead and Copper Rule Improvements page.
The funding conundrum
While public health is a top priority for water utilities, the costs to manage service line inventory and replacement programs can be considerable, and the funding gap strains public water systems aiming for LCRI compliance. The American Water Works Association (AWWA) 2024 State of the Water Industry report confirms that lead and copper are the third largest water quality concern for public water providers, behind PFAS and pathogens. Meanwhile, “financing capital improvements” was considered the second biggest overall challenge to the water sector, with 73.4% of water utilities reporting that they intend to raise rates to afford compliance with the growing list of national drinking water regulations.
The federal government, through the Bipartisan Infrastructure Law (BIL), has allocated $15 billion over the course of five years (2022 - 2026). This funding is available through individual states via their Drinking Water State Revolving Fund (DWSRF) programs. Funds can be used for a variety of projects including programs to identify unknowns and replace service lines. Additionally, 49% of the funding is available as grant funding or principal forgiveness for qualifying communities. Water systems should understand how the funding in each state is being made available and consider if additional funds could enhance their inventory related programs.
Case study: Smyrna, GA, gets expert help managing compliance
After learning about the Lead and Copper Rule Revisions in late 2020, the city of Smyrna, Georgia, wasted no time mapping out its service line inventory. Serving 55,000 residents with approximately 14,000 service connections, Bo Jones, Smyrna’s Director of Water, Sewer and Utilities, did not want to wait for additional state guidance and risk cutting it close to the October 2024 federal compliance deadline. The city worked with 120Water to support its inventory development efforts. After an initial records review including GIS billing data and tap cards kept in a filing cabinet, the city was left with approximately 5,000 unknown service lines.
Additional inventory steps included launching a 1st and 5th liter sampling program that could be used as a tool to help Smyrna prioritize other verification efforts. In addition to sending the sampling kits, notifying customers prior to the kit arriving at the residence was a priority. An educational postcard was sent a few weeks before sending the sampling kits, making residents aware of what was to come. This program sent over 450 informational postcards to customers before sampling and distributed more than 400 sampling kits to homes, along with detailed instructions for sample collection. This process allowed Smyrna to provide customers with an alternative to lawn excavation and helped Smyrna provide strong customer service and build trust throughout the inventory process.
About the Author
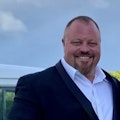
Bo Jones
Bo Jones is the director of water, sewer, and utilities for the city of Smyrna, Georgia.
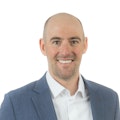
Jonathan Cuppett
Jonathan Cuppett is director of water quality compliance at 120Water.